Find a Carpenter you can trust near you.
Choose from 4824 Carpenters, all rated by people like you.
Over 1720 reviews & an average rating of 4.4/5 stars, you'll find the right pro
Enter your location to refine your search
Choose and shortlist
Use the shortlist button to select up to 4 tradespeople, enter your project details and press send
Keen to get on with the job?
Get up to 4 quotes from local Carpenters near you
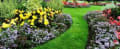



JM Fencing and Landscaping
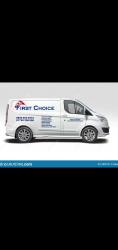



First Choice
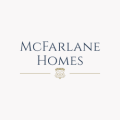


McFarlane Homes
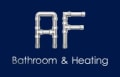


AF bathroom and heating
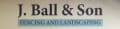



J Ball & SON
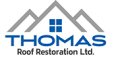



Thomas Roof Restoration
Find a local Carpenter you can trust...
How much do Carpenter services cost?
Do you have a need for a carpenter in or around your house? If yes, then one of the first things you’d probably want to know is the exact amount it would cost to get the project over the line. Now, carpenters are skilled craftsmen that are able to make things with wood and fabricate all sorts of wood constructions. The price charged by carpenters are determined by a wide range of factors which makes it nearly impossible to provide a short and accurate estimate without having a look at your unique requirements. In this post, we’re going to give you an in-depth insight into general carpentry charges while also considering some of the influencing factors. Let’s take a look!
Some of the most common factors that determines the price charged by a carpenter includes the project type, the size as well as scope of the project, the location of project, ease of access, experience and qualification of the carpenter and lots more. For instance, if the job is a minor one such as building a shed, it’ll cost a lot less than something more complex which requires a bit more experience like constructing a staircase. In general, building a shed will have a labour cost within the range of £150 to about £250, while a staircase construction will require a labour cost in between £1,000 to £1,500. For general carpentry, you can expect to pay within the range of £20 to £30 hourly rate depending on a number of factors which are stated above. It’s also important to state that while some carpenters charge per hour, others by the day and several of their projects will be charged at fixed prices.
The table reveals the kinds of work that Carpenters normally do and also the regular cost range of these jobs. Some tasks take longer to finish than others so costs do differ by task.
View our Carpenter cost guide View our Carpenter adviceThe average price
of a Carpenter is:
£1,423
Carpenter job | Carpenter cost in 2025 |
---|---|
Kitchen Fitting | £1,135-£3,714 |
Carpenters and joiners | £365-£3,216 |
Plasterboard dry lining | £315-£863 |
Wood flooring | £750-£1,150 |
Wooden decking | £765-£4,718 |
Garden shed | £497-£1,632 |
Wooden window repair | £190-£577 |
Carpenter service qualifications and accreditations
Carpenters qualifications and also certification's: Having the appropriate training and learning exactly how to do your profession is essential for any trade including Carpenters. View the profile of each Carpenter you are looking at to see what accreditation they hold and also what trade associations they belong to. Some trade associations that Carpenters might possibly be a member of include: HomePro, Federation of Master Builders, Guild of Master Craftsmen. Equally Carpenters might also have the following accreditations: BM TRADA, Chartered Institute of Building, City and Guilds.
Unlike electrical or gas work, carpentry is a different profession where no particular certification is legally required for a carpenter to possess. Generally speaking, the only thing you’ll need so as to practice the trade as well as carry out on site work is to demonstrate your competence as a carpenter. To do this, there’s a number of ways you can consider but one which clearly stands out is to complete a portfolio of work and also earn the NVQ Level 2 Carpentry qualification.
In order to obtain your NVQ Level 2 certification, there’s a need for you to actually learn the trade. You can do this through apprenticeship, working alongside an established carpenter and gradually learning the trade from them. However, it should be noted that it’ll take a couple of years to climb up the ladder from an apprentice to a fully-fledged carpenter. Therefore, if you want to start your new carpentry career sooner rather than later, you might want to consider enrolling on an accredited carpentry training course.
Insurance for Carpenters: Any individual who works in your house, including Carpenters, really should have valid public liability insurance, which safeguards you the house owner and also the Carpenter should unfortunately anything go wrong while they are doing the work. Planning permission for Carpenters Most of the tasks that a Carpenter will do for you will not require planning permission unless its a listed property. Definitely discuss with the Carpenter if planning permission would be needed for the job you are doing, they can suggest the steps that require to be taken.
Services offered by Carpenter
Generally, carpenters are skilled craftsmen who are trained to work in construction as well as cabinet making industry. When it comes to making things with wood, they’re able to fabricate all sorts of wood constructions; from minor projects like custom kitchens or ornate details on wood trim to major ones like carrying out the entire framework of buildings. With that in mind, let’s take a more in depth look at what carpenters does.
In general, carpenters carry out a wide array of unique job duties which depends on whether they work in rough carpentry or finished carpentry. What’s more? There are a number of areas in which carpenters can specialize in special types of wood products or engage in specialized carpentry processes.
For rough carpentry, this typically involves carpenters who work on large scale construction projects where they make use of blueprints to determine the amount as well as type of material required for a job. When they work, they may need to build sleds to haul timber via wooded areas and rough terrain where motorized vehicles cannot access. Finished carpentry, on the other hand, involves carpenters who are skilled in making cabinetry, furniture, models as well as instruments. They’re also able to make ornate, detailed as well as fine wood products for a number of different uses. They must be able to work efficiently on a small scale while also being detailed oriented.
There are a variety of tasks you can employ a Carpenter for, as well as some of one of the most typical jobs that Carpenter are asked to do consist of:
Carpenter FAQs
Properly installed wooden decking will not need a lot of maintenance. Most manufacturers recommend regularly brushing leaves and dirt off the deck, and a yearly cleaning and staining procedure. This will keep the wood in the best condition. Fluids and treatments are readily available from all DIY shops and stores.
Check your Price's door installation cost calculator and charges guide will allow you to estimate both typical labours only costs for door hanging & installations, renovations and repairs as well as the total estimate for comprehensive door installation projects.
• Door & Frame Installation Job and the average Cost in £'s
• uPVC door installation including glazing & architrave costs around £90 per door
• uPVC french & patio door sets including glazing & architrave costs around £120 per pair
• Softwood french & patio door sets including architrave costs around £180 per door
• Hardwood french & patio door sets including architrave would cost around £250 per pair
• Softwood internal door hanging only would be around £40 per door
• Hardwood internal door hanging only would set you back around £48 per door
• Softwood external door hanging only is around £60 per door
• Hardwood external door hanging would cost around £70 per door
• Locks, letterboxes & door furniture timber doors are around £15 per Item
• Glazing £15 per pane
• Brick cut-outs single doors is around £60 per cut-out
• French or patio door brick cut-outs will be around £90 per cut-out
• New lintels will cost around £150 per lintel
Door Repair Costs and Charges
Estimate door mending labour charges by totalling the unit costs of the mandatory jobs. The complete door repair cost includes the total labour charge plus the cost of all parts, fixtures and fittings. A call out charge may be added on jobs totalling less than £100.
Average Cost of Door Repair Job
Replacement glazing units for uPVC doors will be around £15 per unit
Replacement glazing units for timber doors is around £20 per unit
Replacement door glass pined & putty will cost£30 per pane
Replacement handles are around £10 each and general repair work will cost you £25 per hour
Building & FENSA certificate charges
FENSA certificates are obligatory for maximum door replacements and new build setting up prices differ from council to council.
Average Cost of Window Repair Job: One to two doors will cost around £85
Average Cost of Door Fixtures & Fittings Removal Job
Removing internal doors will cost around £10
Removing internal door liners will cost around £15
Removing external timber doors will cost about £10
Removing External timber door frame will be around £20
Removing external uPVC door & frame removal will be around £30 and Rubbish disposal will cost £150 per ton.
- Paving slabs – old or cheap ones are fine
- Timber for the frame and legs
- Type 1 MOT hardcore
- Mark out the area as we explain in ‘How to lay decking’. Then, dig to 200mm below where you want to surface of the decking to be.
- Add a 50mm layer of hardcore and make sure it’s compact.
- Build the decking sub-frame as we describe in ‘How to build a deck frame’.
- Lay out paving slabs along the edges and in the centre of the area. This will help to spread the weight of the decking.
- Set the decking frame on the slabs, checking for high or low points and adding off-cuts of timber where needed. Don’t forget to sand and seal these off-cuts with decking preservative.
- Add your joists and then the deck boards, leaving the recommended gaps of expansion of between 5-8mm.
- Remove any existing fascia boards Remove the fascia boards and the old felt if you’re re-felting.
- Measure the shed roof Measure the roof, taking into account that you should leave around 50mm for overlaps at the eaves and 75mm at the gable ends. You’ll probably need 3 pieces of felt, but some smaller sheds only need 2.
- Apply felt to the roof Once you’ve cut the felt to size, apply the each piece to the roof, pulling it tight. Then nail along the length of the roof at 100mm intervals. For nails at the bottom edge, they can be wider – around 300mm. If you’re adding a piece of felt in the middle of the shed along the apex, fix it using adhesive, then nail it at the lower edge at 50mm intervals.
- Tidy up the overhangs Fold down the felt at each overhang and nail it securely. Cut a slit in the overhang at the apex using a pen knife, then fold that down and nail at 100mm intervals along the gable. If you like, you can add fascia boards to keep the shed looking neat. Use wood nails to secure them and then trim away any excess felt.
- Remove fascias and trims Unscrew or prise off the screws and nails fixing the trims and fascias to your shed.
- Take off doors and remove windows Unscrew hinges from doors and take them off. Remove all metalwork once the door is off. If you’ve got frames on your windows, unscrew these, and remove the panes. Be extra careful if your windows are made of glass.
- Take off the roof Prise off the tacks from the roofing felt and take the felt off – you can’t reuse it, so you’ll need to throw it away. Unscrew the screws on the roof boards and slide them off the shed’s frame – you might need a friend to help you do this.
- Take out the roof brace (optional) If your roof has a brace, unscrew the brackets that hold it to the side of the shed. Remember not to lean on anything once you’ve taken the brace off as the walls might be wobbly.
- Unscrew the frame from the floor Remove all the screws that are holding the shed to the base, remembering not to lean on the walls.
- Unscrew the frame corners Starting at the corner of the front gable, remove the screws where the panels meet. Once a panel is free, lift it carefully out of the way so you can carry on with the others.
When you’re building or redesigning your kitchen, one of the most important decisions you’d have to make is your kitchen cabinets. They are basically where you’ll keep everything you use to cook and as such, take up a lot of space in the kitchen. Therefore, if the aesthetic of your kitchen is a priority, then you’d probably want to get the best quality and good looking cabinet you possibly can. If you’re in the market for new kitchen cabinets, you can put these sources of cabinets into consideration. Let’s take a look!
- IKEA. One of the best place to buy affordable home goods is also a great place to check if you want to buy your kitchen cabinets. According to a research carried out by J.D Power which surveyed over 1500 customers within the past one year, IKEA’s cabinet system ( Sektion) ranked the highest in terms of the overall satisfaction.
- KraftMaid. Another winner of the survey conducted by J.D Power as it took the second position when it comes to the overall satisfaction. Therefore, this store happens to be a good option based on the reviews. This store provides you with a wide variety of colour options to select from, so regardless of what your personal preference is, you’re guaranteed to find something worthwhile to install in your kitchen.
- Stoffer Home. When you buy your kitchen cabinet from an interior designer, there’s a better chance for suitability. Stoffer home offers top quality cabinets which can be manufactured in four various wood finishes and twelve varying paint colours which are all carefully curated.
How To Plasterboard A Wall
If you’re looking to plasterboard your wall, one of the essential things to have in mind is that the plasterboard must be hung horizontally and not vertically. Due to the way they’re manufactured, plasterboard sheets normally possess a “grain along the length. This implies that, it’s only when they’re firmly placed perpendicular against the wall that they’re able to achieve their maximum strength. Materials you’ll need to complete this task includes: Tape measure, stanley knife, pencil, spirit level, drill driver or screw gun, surform, drywall screws and handsaw. Now let’s have a look at the wall plasterboarding steps!
• To plasterboard a wall the first step to take is to place each board in such a way to make the edges the centre of the noggins and upright. Also, the the adjoining walls and door openings should fit closely to the edges.
• Work from the door opening to the ending wall. From the the stud’s edge to the noggin’s centre, use your tape measure to measure a cut board and as a rule to mark up.
• Place your spirit level on the marks and use the Stanley knife to run a line along the intended cut. Once done, turn the board on its edge and give a sharp push on the back to split.
• Cut the paper left with the knife after folding the split edge back on itself. This way, you should get a nice and clean edge.
• In its right position, place the board up against the studwork. Install the screws on the board’s edges where a noggin or upright can be seen.
• Mark lines down across the board at the stud’s centre.
• Cut the end boards to length.
• Install the remaining boards as mentioned above. While doing this, make sure the factory edges are together.
• Cut any board extending into an opening and finish the edges using a surform.
We’d recommend you hire the professional services of a plasterer for the best results especially if you lack the necessary training or experience. Plasterboarding a wall can be a tricky challenge and you’d save yourself some time, money and effort by getting it right on the first trial.
Carpenter help and advice
How it works
Tell us about your Carpenter project
Answer a few quick questions to help us match you with the right Carpenter
Get up to 4 free quotes
Receive no-obligation quotes from 4 Carpenters working in your area.
Pick the right pro for you
Compare prices, customer reviews and services, and hire the right Carpenter.
Are you a Carpenter?
View our open Carpenter jobs near you
Join todayRecent Carpenter Enquiries
Garden | Sheds
Aberdeen - AB11
Enquiry from: Freida A
Start Date: Immediate
Take down shed in kincorth and put it up in Torry 8/6 shed
Garden | Decking
Chepstow - NP16
Enquiry from: George W
Start Date: Immediate



replace existing decking boards, balustrades and steps are you the property owner: owner of the property property type: detached what level of service do you require: supply and deck please call to a...
Carpentry
Shrewsbury - SY5
Enquiry from: Jan M
Start Date: 1 to 3 months
hi i have received quote from paul woollam for windows along with your number for window fitting. we would be fitting 9 sash windows and 5 casement windows. as mentioned to paul we would be happy with...
Garden | Decking
Bucknell, Craven Arms, Lydbury North - SY7
Enquiry from: David M
Start Date: Immediate
4 x 5 metre decking to be laid
Garden | Decking
Glossop - SK13
Enquiry from: Richard P
Start Date: Immediate
I would like to get a quote for the removal & disposal of existing wooden decking, and the supply & installation of new composite, or PVC. Decking. The area concerned *** wide (2.13mt) x 20ft long (6...
Garden | Decking
Newton Stewart - DG8
Enquiry from: Bob M
Start Date: Immediate



Caravan decking needs replaced
Garden | Sheds
Chester le Street - DH3
Enquiry from: John B
Start Date: Immediate
1 shed supplied & erected.
Garden | Decking
Looe - PL13
Enquiry from: Susan G
Start Date: Immediate
Small decking area approx 6'x4'
Garden | Sheds
Enfield - EN1
Enquiry from: Muharrem H
Start Date: Immediate
i have a metal shed and i want to attach a second smaller shed to it. is this something you can do? are you the property owner: owner of the property do you have a: large garden what level of service ...
Garden | Decking
Portsmouth - PO6
Enquiry from: Joseph M
Start Date: Immediate
decking steps are becoming lose. are you the property owner: tenant (with permission) property type: terrace what level of service do you require: supply and deck please call to appoint
Garden | Decking
Morpeth - NE65
Enquiry from: Elisabeth B
Start Date: Immediate
Remove old wood decking replace with composite decking
Carpentry
Chorley - PR7
Enquiry from: Jim W
Start Date: Immediate
We require a New Staircase 7 Fire doors fitted Loft ladder fitted
Carpentry
High Peak - SK23
Enquiry from: Keren G
Start Date: Immediate
I'm wanting my existing stairs changed to light oak
Garden | Decking
Bromley, Keston - BR2
Enquiry from: Brian C
Start Date: Immediate




cleaning/sanding and a protective coating for existing wooden decking and a balustrade, plus replacement of broken boards. advice on future treatment. on-site parking is available. are you the pro...
Flooring | Wooden
Wakefield - WF4
Enquiry from: Don B
Start Date: Immediate
Re joist and board 6 foot square (approx) bathroom.
Garden | Decking
Nottingham, Sutton-in-Ashfield - NG17
Enquiry from: Andrew S
Start Date: Immediate
Removal of old slabs and fitting of wooden decking at bottom of garden. Approx area 30square metres.
Garden | Decking
St. Helens - WA9
Enquiry from: Vivienne B
Start Date: Immediate
Measure supply and lay composite decking
Garden | Decking
Newquay - TR7
Enquiry from: Morgan E
Start Date: Immediate
I am looking to replace my current decking, like for like, as it has rotten. The decking is about 6m x 5m and split over two levels, with four steps (I can send you images of the floorplan)
Garden | Decking
Inverurie - AB51
Enquiry from: Elaine M
Start Date: Immediate
removal of old wooden decking and supply and installation of composite decking are you the property owner: owner of the property property type: detached what level of service do you require: supply an...
Garden | Decking
Wednesbury - WS10
Enquiry from: Ashley N
Start Date: Immediate
Back garden wood decking
Carpenter in your region
- Carpenter Scotland
- Carpenter Northern Ireland
- Carpenter North East
- Carpenter North West
- Carpenter East Midlands
- Carpenter West Midlands
- Carpenter Wales
- Carpenter South West
- Carpenter South East
- Carpenter Greater London
- Carpenter Isle of Man
- Carpenter Channel Islands
- Carpenter Yorkshire & Humberside
- Carpenter East Anglia