Yes, your shed does need a base. This is to give it a solid, level foundation. Open soil will not help with the longevity of the shed itself or the contents within. The best materials to use to make your shed base are concrete, natural stone or wood.
Find a Carpenter you can trust near you.
Choose from 4824 Carpenters, all rated by people like you.
Over 1720 reviews & an average rating of 4.4/5 stars, you'll find the right pro
Enter your location to refine your search
Choose and shortlist
Use the shortlist button to select up to 4 tradespeople, enter your project details and press send
Keen to get on with the job?
Get up to 4 quotes from local Carpenters near you
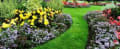



JM Fencing and Landscaping
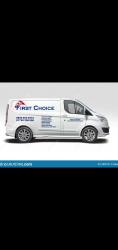



First Choice
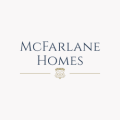


McFarlane Homes
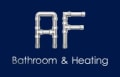


AF bathroom and heating
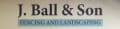



J Ball & SON
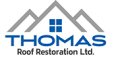



Thomas Roof Restoration
Find a local Carpenter you can trust...
How much do Carpenter services cost?
Do you have a need for a carpenter in or around your house? If yes, then one of the first things you’d probably want to know is the exact amount it would cost to get the project over the line. Now, carpenters are skilled craftsmen that are able to make things with wood and fabricate all sorts of wood constructions. The price charged by carpenters are determined by a wide range of factors which makes it nearly impossible to provide a short and accurate estimate without having a look at your unique requirements. In this post, we’re going to give you an in-depth insight into general carpentry charges while also considering some of the influencing factors. Let’s take a look!
Some of the most common factors that determines the price charged by a carpenter includes the project type, the size as well as scope of the project, the location of project, ease of access, experience and qualification of the carpenter and lots more. For instance, if the job is a minor one such as building a shed, it’ll cost a lot less than something more complex which requires a bit more experience like constructing a staircase. In general, building a shed will have a labour cost within the range of £150 to about £250, while a staircase construction will require a labour cost in between £1,000 to £1,500. For general carpentry, you can expect to pay within the range of £20 to £30 hourly rate depending on a number of factors which are stated above. It’s also important to state that while some carpenters charge per hour, others by the day and several of their projects will be charged at fixed prices.
The table reveals the kinds of work that Carpenters normally do and also the regular cost range of these jobs. Some tasks take longer to finish than others so costs do differ by task.
View our Carpenter cost guide View our Carpenter adviceThe average price
of a Carpenter is:
£1,423
Carpenter job | Carpenter cost in 2025 |
---|---|
Kitchen Fitting | £1,135-£3,714 |
Carpenters and joiners | £365-£3,216 |
Plasterboard dry lining | £315-£863 |
Wood flooring | £750-£1,150 |
Wooden decking | £765-£4,718 |
Garden shed | £497-£1,632 |
Wooden window repair | £190-£577 |
Carpenter service qualifications and accreditations
Carpenters qualifications and also certification's: Having the appropriate training and learning exactly how to do your profession is essential for any trade including Carpenters. View the profile of each Carpenter you are looking at to see what accreditation they hold and also what trade associations they belong to. Some trade associations that Carpenters might possibly be a member of include: HomePro, Federation of Master Builders, Guild of Master Craftsmen. Equally Carpenters might also have the following accreditations: BM TRADA, Chartered Institute of Building, City and Guilds.
Unlike electrical or gas work, carpentry is a different profession where no particular certification is legally required for a carpenter to possess. Generally speaking, the only thing you’ll need so as to practice the trade as well as carry out on site work is to demonstrate your competence as a carpenter. To do this, there’s a number of ways you can consider but one which clearly stands out is to complete a portfolio of work and also earn the NVQ Level 2 Carpentry qualification.
In order to obtain your NVQ Level 2 certification, there’s a need for you to actually learn the trade. You can do this through apprenticeship, working alongside an established carpenter and gradually learning the trade from them. However, it should be noted that it’ll take a couple of years to climb up the ladder from an apprentice to a fully-fledged carpenter. Therefore, if you want to start your new carpentry career sooner rather than later, you might want to consider enrolling on an accredited carpentry training course.
Insurance for Carpenters: Any individual who works in your house, including Carpenters, really should have valid public liability insurance, which safeguards you the house owner and also the Carpenter should unfortunately anything go wrong while they are doing the work. Planning permission for Carpenters Most of the tasks that a Carpenter will do for you will not require planning permission unless its a listed property. Definitely discuss with the Carpenter if planning permission would be needed for the job you are doing, they can suggest the steps that require to be taken.
Services offered by Carpenter
Generally, carpenters are skilled craftsmen who are trained to work in construction as well as cabinet making industry. When it comes to making things with wood, they’re able to fabricate all sorts of wood constructions; from minor projects like custom kitchens or ornate details on wood trim to major ones like carrying out the entire framework of buildings. With that in mind, let’s take a more in depth look at what carpenters does.
In general, carpenters carry out a wide array of unique job duties which depends on whether they work in rough carpentry or finished carpentry. What’s more? There are a number of areas in which carpenters can specialize in special types of wood products or engage in specialized carpentry processes.
For rough carpentry, this typically involves carpenters who work on large scale construction projects where they make use of blueprints to determine the amount as well as type of material required for a job. When they work, they may need to build sleds to haul timber via wooded areas and rough terrain where motorized vehicles cannot access. Finished carpentry, on the other hand, involves carpenters who are skilled in making cabinetry, furniture, models as well as instruments. They’re also able to make ornate, detailed as well as fine wood products for a number of different uses. They must be able to work efficiently on a small scale while also being detailed oriented.
There are a variety of tasks you can employ a Carpenter for, as well as some of one of the most typical jobs that Carpenter are asked to do consist of:
Carpenter FAQs
How Much Is Plasterboard?
Do you wish to install plasterboard in the nearest future? If yes, then you’d probably want to know the amount it’s going to cost. Here, we’ll give you a detailed plasterboarding prices breakdown to help you calculate an estimate for your project.
A plasterboarding project including the cost of both materials and labour with the use of a high quality panels is about £4 to £5 per panel. Therefore, if you wish to calculate on the basis of a standard room about 12x12ft would cost about £500 to £600. However, this price can fluctuate significantly depending on the professional as well as the quality of the materials you wish to incorporate in completing the project. We’d recommend that you hire the services of a professional with accreditation as he would provide you with a detailed quote with no hidden charges or costs. To give you a clearer idea, we’ve taken the time out to put together some estimated costs of employing the services of a seasoned professional plasterer to supply and plasterboard your home or office. Let’s take a look!
• A 6 x 12ft room with panels and plasterboard should have an average cost within the range of £250 to £400 and duration of one to two days.
• The individual cost of plasterboarding or drywalling a standard 12 x 12ft room should have an average cost within the range of £500 to £600 and duration of one to three days. These includes 60% for materials used (£330), 30% for tradespersons (£165) and the remaining 10% for waste removal (£55) to give a total cost of £550.
• A 12 x 24ft room with panels and plasterboard should have an average cost within the range of £1000 to £1200 and duration of three to six days.
Do you have existing floorboards and wish to fit new solid wood floor over it? If you’re planning to go for a DIY effort, there are a number of things you should put into consideration before you even get started. Firstly, you should have it in mind that existing softwood floorboards are usually not flat, implying that the surface of the existing might not be ideal to serve as the foundation on which to put your new solid wood flooring. Secondly, if you’re going to lay the new solid floor on the existing floorboards, it would be wise to select wood that is a minimum of 18mm thick to make your new solid wood flooring a lot more stable.
If you discover that your old floor is not too even, there are two option you can consider to protect your investment. You can lay the new floor at a 90 degree angle over the existing one. In other words, you should lay the new floor lengthways if the old one is laid widthways. Using this technique alongside a method of fitting referred to as secret nailing will go a long way to make sure your installation efforts is a successful one.
The second option you can put into consideration when laying solid wood flooring over old ones is to lay chipboard or plywood over the existing floor prior to the installation of the new floor. Here, there will be an increase in the cost of your installation, however it will be more reliable and durable as it assists in ensuring the stability of your new flooring. Some benefits that comes with this option includes the freedom to lay the new solid wood flooring in any direction you want as well as the freedom to use any fitting method you deem fit. Click here to learn more about wood flooring.
The cost of just the engineered wood flooringis from £18 to £73 per m2.
- If you’ve not got an overhang or it’s a fixed deck, fit starter clips along the outside edge of the frame and secure with screws provided with the composite decking. If you are working with an overhang, put the first board into position not exceeding 25mm. If you’re adding a fascia, put an off-cut of board under the overhang so you know it’ll be flush with the fascia.
- Pre-drill all fixing points, measuring in 30mm from the edge of the board. Secure the board to the joist below with composite decking screws.
- Slide a hidden fastener clip in so it sits within the groove of the deck board. It needs to be in the centre of the joist to keep the boards secure and ensure an expansion gap of 6mm. Tighten the clips until just tight, and repeat so there’s a clip at every joist.
- Add the next board, ensuring that the fastener clips sit within the groove – make sure you don’t force it. Repeat step 3.
- Continue steps 3 and 4 until you’re at the final board, which you should secure in the same way as you did the first.
Being the primary material used in wooden flooring installation, the floorboards are the main supply costs. With that in mind, you should also know that there are a large variety of wooden flooring types to select from, each with their unique pros and cons which should all be considered before making a purchase decision. If you’re looking to get the supply cost of wooden flooring in the UK, then you’ve come to the right place! Here is a basic price guide of various and some of the most popular types of floorboards.
If you wish to go for an engineered wood flooring, this looks better when compared to laminate and is more affordable than solid wood. You can expect to pay within the range of £20 to about £100 per square metre for this wood flooring type.
Laminate flooring, on the other hand, is also quite cheap, easy to install and quite hardwearing, however it tends to warp over time as a result of exposure to moisture and it also happens to be the least attractive of all the other flooring types. You can expect to pay within the range of £10 to about £50 per square metre for this wood flooring type.
Solid wood flooring is a great option with a better look and feel to it. However, it also tends to warp over time and more difficult to install as against laminate. You can expect to pay within the range of £20 to about £100 per square metre for this wood flooring type.
Parquet flooring is long lasting and very attractive, but quite expensive to have fitted. You can expect to pay within the range of £25 to about £200 per square metre for this wood flooring type.
How To Dot And Dab A Plasterboard
If you want a fast and simple way to achieve a smooth and sturdy wall which is decoration-ready, then dot and dab plasterboard is the way to go! It’s a relative simple process but can also be a bit challenging. Therefore, if you lack the necessary training or experience, hiring a professional would be a great step to protect your investment and guarantee the best results. Here, we’ll provide you with a deep insight into the plasterboard’s dot and dab procedures. Let’s have a look!
• At the thickness of the board with the adhesive, mark the ceiling and floor as well as the wall to indicate the centre of each board.
• Ensure the wall’s height is 15mm more than the plasterboard
• Make a mixture of the adhesive and achieve a thick consistency. Apply a consistent layer of the mixture around the wall’s perimeter, edge of the ceiling and any other openings with the use of a trowel.
• Select dabs that are about 250mm long and 50mm to 75mm wide and apply the adhesive in them. Make use of 3 vertical rows for individual boards. Also ensure to apply, at skirting level, a band of adhesive.
• Position the board’s reverse side against the dabs, and laying against the packers. Then make the board align with the ceiling and floor marks with the help of a straight edge.
• Raise the board till its tight against the ceiling with a board lifter. Once done, use the plasterboard to wedge the board into place before you remove the board lifter.
• Repeat the same process for the remaining parts of the room. Once completed, make sure the adhesive is set before you remove the boards.
- What you need the shed for
- How much space you have
- How big you need the shed to be
- Which style of roof you want
- What material you would like
- How big your budget is
- Hand-crafted from Nordic White Spruce
- Felt roof reinforced with high-grade polyester
- Tongue and groove cladding makes it more weatherproof so ideal for items that must be kept dry
- High eaves for more head height and to store taller items
- Pent roof and fixed windows allow lots of light
- Ideal for putting up against a wall or fence
- Door can be hinged either side
- Ideal for small gardens or those with fewer tools to store
- Apex roof for water runoff
- Tongue and groove walls
- Tall floor-to-gable door
Carpenter help and advice
How it works
Tell us about your Carpenter project
Answer a few quick questions to help us match you with the right Carpenter
Get up to 4 free quotes
Receive no-obligation quotes from 4 Carpenters working in your area.
Pick the right pro for you
Compare prices, customer reviews and services, and hire the right Carpenter.
Are you a Carpenter?
View our open Carpenter jobs near you
Join todayRecent Carpenter Enquiries
Garden | Sheds
Aberdeen - AB11
Enquiry from: Freida A
Start Date: Immediate
Take down shed in kincorth and put it up in Torry 8/6 shed
Garden | Decking
Chepstow - NP16
Enquiry from: George W
Start Date: Immediate



replace existing decking boards, balustrades and steps are you the property owner: owner of the property property type: detached what level of service do you require: supply and deck please call to a...
Carpentry
Shrewsbury - SY5
Enquiry from: Jan M
Start Date: 1 to 3 months
hi i have received quote from paul woollam for windows along with your number for window fitting. we would be fitting 9 sash windows and 5 casement windows. as mentioned to paul we would be happy with...
Garden | Decking
Bucknell, Craven Arms, Lydbury North - SY7
Enquiry from: David M
Start Date: Immediate
4 x 5 metre decking to be laid
Garden | Decking
Glossop - SK13
Enquiry from: Richard P
Start Date: Immediate
I would like to get a quote for the removal & disposal of existing wooden decking, and the supply & installation of new composite, or PVC. Decking. The area concerned *** wide (2.13mt) x 20ft long (6...
Garden | Decking
Newton Stewart - DG8
Enquiry from: Bob M
Start Date: Immediate



Caravan decking needs replaced
Garden | Sheds
Chester le Street - DH3
Enquiry from: John B
Start Date: Immediate
1 shed supplied & erected.
Garden | Decking
Looe - PL13
Enquiry from: Susan G
Start Date: Immediate
Small decking area approx 6'x4'
Garden | Sheds
Enfield - EN1
Enquiry from: Muharrem H
Start Date: Immediate
i have a metal shed and i want to attach a second smaller shed to it. is this something you can do? are you the property owner: owner of the property do you have a: large garden what level of service ...
Garden | Decking
Portsmouth - PO6
Enquiry from: Joseph M
Start Date: Immediate
decking steps are becoming lose. are you the property owner: tenant (with permission) property type: terrace what level of service do you require: supply and deck please call to appoint
Garden | Decking
Morpeth - NE65
Enquiry from: Elisabeth B
Start Date: Immediate
Remove old wood decking replace with composite decking
Carpentry
Chorley - PR7
Enquiry from: Jim W
Start Date: Immediate
We require a New Staircase 7 Fire doors fitted Loft ladder fitted
Carpentry
High Peak - SK23
Enquiry from: Keren G
Start Date: Immediate
I'm wanting my existing stairs changed to light oak
Garden | Decking
Bromley, Keston - BR2
Enquiry from: Brian C
Start Date: Immediate




cleaning/sanding and a protective coating for existing wooden decking and a balustrade, plus replacement of broken boards. advice on future treatment. on-site parking is available. are you the pro...
Flooring | Wooden
Wakefield - WF4
Enquiry from: Don B
Start Date: Immediate
Re joist and board 6 foot square (approx) bathroom.
Garden | Decking
Nottingham, Sutton-in-Ashfield - NG17
Enquiry from: Andrew S
Start Date: Immediate
Removal of old slabs and fitting of wooden decking at bottom of garden. Approx area 30square metres.
Garden | Decking
St. Helens - WA9
Enquiry from: Vivienne B
Start Date: Immediate
Measure supply and lay composite decking
Garden | Decking
Newquay - TR7
Enquiry from: Morgan E
Start Date: Immediate
I am looking to replace my current decking, like for like, as it has rotten. The decking is about 6m x 5m and split over two levels, with four steps (I can send you images of the floorplan)
Garden | Decking
Inverurie - AB51
Enquiry from: Elaine M
Start Date: Immediate
removal of old wooden decking and supply and installation of composite decking are you the property owner: owner of the property property type: detached what level of service do you require: supply an...
Garden | Decking
Wednesbury - WS10
Enquiry from: Ashley N
Start Date: Immediate
Back garden wood decking
Carpenter in your region
- Carpenter Scotland
- Carpenter Northern Ireland
- Carpenter North East
- Carpenter North West
- Carpenter East Midlands
- Carpenter West Midlands
- Carpenter Wales
- Carpenter South West
- Carpenter South East
- Carpenter Greater London
- Carpenter Isle of Man
- Carpenter Channel Islands
- Carpenter Yorkshire & Humberside
- Carpenter East Anglia