- Remove fascias and trims Unscrew or prise off the screws and nails fixing the trims and fascias to your shed.
- Take off doors and remove windows Unscrew hinges from doors and take them off. Remove all metalwork once the door is off. If you’ve got frames on your windows, unscrew these, and remove the panes. Be extra careful if your windows are made of glass.
- Take off the roof Prise off the tacks from the roofing felt and take the felt off – you can’t reuse it, so you’ll need to throw it away. Unscrew the screws on the roof boards and slide them off the shed’s frame – you might need a friend to help you do this.
- Take out the roof brace (optional) If your roof has a brace, unscrew the brackets that hold it to the side of the shed. Remember not to lean on anything once you’ve taken the brace off as the walls might be wobbly.
- Unscrew the frame from the floor Remove all the screws that are holding the shed to the base, remembering not to lean on the walls.
- Unscrew the frame corners Starting at the corner of the front gable, remove the screws where the panels meet. Once a panel is free, lift it carefully out of the way so you can carry on with the others.
Find a Carpenter you can trust in Belford.
Choose from 59 Carpenters, all rated by people like you.
Over 28 reviews & an average rating of 4.7/5 stars, you'll find the right pro
Choose and shortlist
Use the shortlist button to select up to 4 tradespeople, enter your project details and press send
Keen to get on with the job?
Get up to 4 quotes from local Carpenters near you
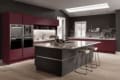

Haus 12 Interior
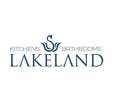

Lakeland Kitchens and Bathrooms
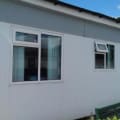

LNB Services


Toplineroofing & gutters
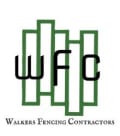

Walkers fencing contractors
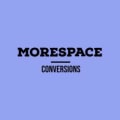

Morespace conversions NE
How much do Carpenter services cost?
Do you have a need for a carpenter in or around your house? If yes, then one of the first things you’d probably want to know is the exact amount it would cost to get the project over the line. Now, carpenters are skilled craftsmen that are able to make things with wood and fabricate all sorts of wood constructions. The price charged by carpenters are determined by a wide range of factors which makes it nearly impossible to provide a short and accurate estimate without having a look at your unique requirements. In this post, we’re going to give you an in-depth insight into general carpentry charges while also considering some of the influencing factors. Let’s take a look!
Some of the most common factors that determines the price charged by a carpenter includes the project type, the size as well as scope of the project, the location of project, ease of access, experience and qualification of the carpenter and lots more. For instance, if the job is a minor one such as building a shed, it’ll cost a lot less than something more complex which requires a bit more experience like constructing a staircase. In general, building a shed will have a labour cost within the range of £150 to about £250, while a staircase construction will require a labour cost in between £1,000 to £1,500. For general carpentry, you can expect to pay within the range of £20 to £30 hourly rate depending on a number of factors which are stated above. It’s also important to state that while some carpenters charge per hour, others by the day and several of their projects will be charged at fixed prices.
The table reveals the kinds of work that Carpenters normally do and also the regular cost range of these jobs. Some tasks take longer to finish than others so costs do differ by task.
View our Carpenter cost guide View our Carpenter adviceThe average price
of a Carpenter in Belford is:
£879
Carpenter job | Carpenter cost in 2025 |
---|---|
Kitchen Fitting in Belford | £975-£2,495 |
Carpenters and joiners in Belford | £375-£575 |
Plasterboard dry lining in Belford | £638-£978 |
Wood flooring in Belford | £750-£1,150 |
Wooden decking in Belford | £1,125-£1,725 |
Garden shed in Belford | £450-£690 |
Wooden window repair in Belford | £320-£480 |
Carpenter FAQs
- Tongue and groove timber boards
- Boards for the ledges and braces, at least 20mm thick
- Nails
- Hammer
- Saws, including a circular saw
- Chisel
- Mallet
- Cut your boards to size If you can’t buy boards at the right height and width for your door, cut the boards to length using a circular saw. Don’t forget to sand and treat any cut ends with timber preservative. Lay out the boards in the best arrangement for your shed door, with the inside of the door facing up.
- Arrange the ledges and braces On most shed doors, you’ll probably need 3 boards across the back of the door to form the ledges. The ledges keep the door straight and keep the boards of the door together. The braces are the parts of the door that slope down to form a ‘Z’ shape between the ledges. Ensure that the braces are sloped up from the bottom and middle hinge to stop the door from sagging as the timber expands and contracts in the weather. Once you’re happy with the arrangement, mark the spots on the boards where they will meet and cut out of the housings using a chisel and mallet.
- Put the door together Use clamps to pull the boards together and hold the ledges and braces in place. Nail from the front of the door through the boards and ledges to fix them. Secure the ledges and braces with screws; you may want to pre-drill and countersink holes to prevent the wood from splitting. Remember to treat them with preservative if you do.
- Fix the shed door hinges Make sure you measure carefully before attaching the hinges, ensuring you know where the pin sits in relation to where the door opens.
- Treat the door and add locks and handles Apply some wood oil, like linseed or teak oil, to help prevent water damage. Then add locks or handles to your shed to help keep it secure. If you’d rather leave it to the professionals, there are plenty of specialists that will be able to make a shed door for you, or even put up an entire shed.
Considerations
If you're thinking about making changes around your household that include working with wood, you ought to hire a local carpenter. Looking to fix a loose piece? Or looking for some drastic improvements? A carpentry expert might be the top choice.
General carpenters are expert woodsmen and know a variety of areas from grounds to gear. Maximum carpentry depends on a rudimentary set of skills which your worker may choose to build upon by specialising. For example, few carpenters have a talent for wood repair, building original constructions or manufacturing furniture.
Time
The extent of time it takes to complete a certain project is another consideration to be kept in mind. This is particularly essential if you are on a constricted timeline or dealing with time limitations. Most carpentry projects take about 13 hours to finish. Although, this is purely dependent on the intricacy of the project and the pre-arranged timeline you and your carpenter agree to.
The cost to hire a general carpenter in the UK amounts to £20 to £25 per hour on an average. Though, it is always imperative to speak with a professional in carpentry services about this.
General Carpentry Costs in the UK:
• National Minimum Cost is £20
• National Maximum Cost is £25
• The national average is around £22
Cost Comparison of Popular Carpentry Services in the UK (Average Hourly Rate):
• Furniture Refinishing is around £17
• A Cabinet Repair is around £23
• Finish Carpentry will set you back a minimum of £30
• General Carpentry is around £20
• Fine Woodworking is about £20
Carpentry is a brilliant method to improve your household and to help maintain its visual pleasantness. Finding a decent carpenter at the correct value is a vital area that needs undivided attention in terms of your project. Whether you're reinforcing your staircase or looking for a total renovation of the house that would change its look, a general carpenter will complete your project to the highest standards.
- Decking joists
- Coach screws
- Coach bolts
- Combi drill
- Socket set
- A saw suitable for your project and the thickness of the timber
- Pencil
- Decking preservative
- Sandpaper or sander
- Measure your deck frame and cut to size if necessary.
- Make 2 pencil marks on each end of the frame’s 2 outer joists to mark where the coach screws will go. They need to align with the centre of the adjoining outer joist. Then, use a flat wood drill bit to drill recesses into each mark. Make them the same depth of the screws that your using’s head and wide enough for a ratchet or socket to tighten them.
- Using a thinner drill bit, line up the outer joists and drill a pilot hole through the middle of the recess. These pilot holes act as a guide for the screws and stops them from splitting the wood.
- Fit the coach screws with either a drill driver or socket and ratchet.
- Repeat the process for the inner joists once you’ve assembled the outer frame.
- If you’ve not got an overhang or it’s a fixed deck, fit starter clips along the outside edge of the frame and secure with screws provided with the composite decking. If you are working with an overhang, put the first board into position not exceeding 25mm. If you’re adding a fascia, put an off-cut of board under the overhang so you know it’ll be flush with the fascia.
- Pre-drill all fixing points, measuring in 30mm from the edge of the board. Secure the board to the joist below with composite decking screws.
- Slide a hidden fastener clip in so it sits within the groove of the deck board. It needs to be in the centre of the joist to keep the boards secure and ensure an expansion gap of 6mm. Tighten the clips until just tight, and repeat so there’s a clip at every joist.
- Add the next board, ensuring that the fastener clips sit within the groove – make sure you don’t force it. Repeat step 3.
- Continue steps 3 and 4 until you’re at the final board, which you should secure in the same way as you did the first.
Installing wooden flooring is a quite simple process, however to get it right the first time, there are very essential preparations that must be made. These includes determining the site is in the best condition before installation, removal of all floor coverings and underlay for a more stable and durable installation and incorporation of the right expansion gap of about 10mm to 12mm which would be maintained around the floor’s perimeter.
Wooden floor fitting can be done on two types of sub-floor - Concrete and Plywood. To install onto concrete, you can follow the guide below:
• Incorporate flexible wood on concrete adhesives.
• With the help of a 3mm toothed trowel, spread above 2 board widths of adhesive along the starting wall sub-floor, beginning at a corner of your room.
• Position the first row of flooring into the area that is glued using the tongue facing opposite the wall.
• Put 10mm spacers against the wall to see to the consistency in expansion gaps.
• Make sure the joints are at a minimum of 150mm apart from the first row when fitting the second row.
• Utilize pre-cut smaller boards if you’re to start a new row with staggered joints.
• Continue with this nailing method and make sure the 10mm expansion gaps are consistent around the floor’s perimeter.
To install onto plywood, you can follow this guide:
• Make use of a porta-nailer.
• Position 10mm spacers against the wall - parallel with the installation direction.
• Fit the first row using the tongue facing opposite the wall and with the help of the porta-nailer or flooring nailer.
• Lay the second row and make sure the short end joints are at a minimum of 150mm apart from that of the first row.
• Utilize pre-cut smaller boards if you’re to start a new row with staggered joints.
• Continue with this nailing method and make sure the 10mm expansion gaps are consistent around the floor’s perimeter.
Click here to learn more about wood flooring.
Though both solid wood and engineered wood can be installed on a concrete sub-floor, the processes are quite different from each other. Solid wood is produced from a single plank of wood which can be reactive to both temperature and humidity changes which is capable of making the wood expand or contract. Hence, the different approach to solid wood and engineered wood flooring installation on concrete. Here, we’ll discuss how you can lay solid wood on your concrete.
First and foremost, you’d have to determine the method you’ll use to attach the planks to the floor. Is it floating whereby you only have to lay the wood flooring on the concrete after fitting the right underlay? You can also go for the most popular installation method which is gluing your floor with a flexible wood adhesive (to be applied to both the boards and the sub-floor). Or perhaps you’d prefer to use the traditional method of nailing the boards to the concrete (the nails will be covered as you lay the subsequent planks and the groove locks with the tongue).
After making this decision, you’d have to ensure that the sub-floor is well prepared for the installation. This implies checking the wood’s moisture content (mustn’t exceed 7 to 8 percent). Also inspect the floor to ensure its neat, if not, clear out the dirt or debris and make sure the surface is flat to avoid post-installation problems.
In the event whereby you discover a high moisture content, you’d want to acquire a damp proof membrane. This will not only enhance the floor’s stability, but also prevent shrinking or warping of the wood due to changes in humidity or temperature.
It is crucial to note that the preparation of the sub-floor is equally as important as the laying of the planks as this can go a long way to improve the durability and strength of your floor. Click here to learn more about wood flooring.
How Much Plasterboard Do I Need?
Although many people especially contractors have a tough time estimating the number of drywall or plasterboard needed to complete a project, it’s a rather simple task if all factors are taken into consideration. If you’re able to follow the same procedures taken by professionals to count dry wall sheets, you’ll be in the right direction. Let’s have a look at the procedures to follow!
lTake Square Footage Measurement
• Measure the square footage of the area where the plasterboard will be fitted.
• Multiply the height by the width of each wall or ceiling area.
• Add all quantities to obtain a total square-foot amount.
lCalculate Drywall Sheets
• To calculate the number of drywall or plasterboard sheet is very simple once you’ve gotten the total square footage.
• To get started, simply divide the total square footage of area by 32 (that’s if you are using a 4 by 8 sheets) or you can also make use of 48 to make the division (only if you’re making use of the 4 by 12 sheets).
• The answer you get after the division will give you the full number of plasterboard sheets that’s required to complete the project.
We’d recommend you include an extra 10 to 15 percent of whatever you calculate to take care of the possible odd cuts and wastages. This implies that if your total area is 1600 square feet while incorporating 4 by 8 sheets, simply divide 1600 by 32 which equals 50 sheets, now take 10% of 50 which equals 5, then add back the 5 extra to the 50 sheets earlier calculated to get 55 sheets. If you wish to estimate the cost, simply multiply the number of sheets gotten by the price per sheet. Do not forget to include delivery charges and local taxes.
Carpenter help and advice
How it works
Tell us about your Carpenter project
Answer a few quick questions to help us match you with the right Carpenter
Get up to 4 free quotes
Receive no-obligation quotes from 4 Carpenters working in Belford.
Pick the right pro for you
Compare prices, customer reviews and services, and hire the right Carpenter.
Are you a Carpenter in Belford?
View our open Carpenter jobs near you
Join today