The cost of just the engineered wood flooringis from £18 to £73 per m2.
Find a Carpenter you can trust in Settle.
Choose from 145 Carpenters, all rated by people like you.
Over 104 reviews & an average rating of 4.6/5 stars, you'll find the right pro
Choose and shortlist
Use the shortlist button to select up to 4 tradespeople, enter your project details and press send
Keen to get on with the job?
Get up to 4 quotes from local Carpenters near you
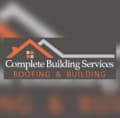

Yorkshire Drives Patios & Landscapes
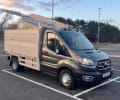

Tree fellers tree surgery
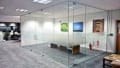

Martin costello joinery services
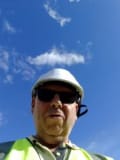

Work from home
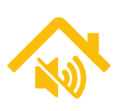

Yorkshire Soundproofing
How much do Carpenter services cost?
Do you have a need for a carpenter in or around your house? If yes, then one of the first things you’d probably want to know is the exact amount it would cost to get the project over the line. Now, carpenters are skilled craftsmen that are able to make things with wood and fabricate all sorts of wood constructions. The price charged by carpenters are determined by a wide range of factors which makes it nearly impossible to provide a short and accurate estimate without having a look at your unique requirements. In this post, we’re going to give you an in-depth insight into general carpentry charges while also considering some of the influencing factors. Let’s take a look!
Some of the most common factors that determines the price charged by a carpenter includes the project type, the size as well as scope of the project, the location of project, ease of access, experience and qualification of the carpenter and lots more. For instance, if the job is a minor one such as building a shed, it’ll cost a lot less than something more complex which requires a bit more experience like constructing a staircase. In general, building a shed will have a labour cost within the range of £150 to about £250, while a staircase construction will require a labour cost in between £1,000 to £1,500. For general carpentry, you can expect to pay within the range of £20 to £30 hourly rate depending on a number of factors which are stated above. It’s also important to state that while some carpenters charge per hour, others by the day and several of their projects will be charged at fixed prices.
The table reveals the kinds of work that Carpenters normally do and also the regular cost range of these jobs. Some tasks take longer to finish than others so costs do differ by task.
View our Carpenter cost guide View our Carpenter adviceThe average price
of a Carpenter in Settle is:
£898
Carpenter job | Carpenter cost in 2025 |
---|---|
Kitchen Fitting in Settle | £975-£2,495 |
Carpenters and joiners in Settle | £375-£575 |
Plasterboard dry lining in Settle | £444-£1,489 |
Wood flooring in Settle | £750-£1,150 |
Wooden decking in Settle | £1,125-£1,725 |
Garden shed in Settle | £450-£690 |
Wooden window repair in Settle | £320-£480 |
Carpenter FAQs
- What you need the shed for
- How much space you have
- How big you need the shed to be
- Which style of roof you want
- What material you would like
- How big your budget is
- Hand-crafted from Nordic White Spruce
- Felt roof reinforced with high-grade polyester
- Tongue and groove cladding makes it more weatherproof so ideal for items that must be kept dry
- High eaves for more head height and to store taller items
- Pent roof and fixed windows allow lots of light
- Ideal for putting up against a wall or fence
- Door can be hinged either side
- Ideal for small gardens or those with fewer tools to store
- Apex roof for water runoff
- Tongue and groove walls
- Tall floor-to-gable door
What Is Plasterboard?
The plasterboard is unarguably one of the most common building materials across the globe. Sometimes referred to as gypsum board, gyprock, drywall or wall board, the plasterboard is mostly incorporated for ceiling cladding and interior walls in several homes and offices in recent times. However, despite its global acceptability, it’s a very misunderstood building material.
The plasterboard is manufactured using a gypsum core with a heavy paper covering both sides of the sheet. The measurement of a standard plasterboard sheet is a length of 2.4 metres in and a width of 1.2 metres, with a thickness of about 13mm. The board usually have either a bevelled or a bit flat edge. The bevelled edge makes it easy for the installers to use a plaster to smooth out the surface after nailing the sheets to walls and ceilings as well as taping the edges.
The plasterboard comes in different types. Although various manufacturers provide a unique name for their products, but they’re all included in one of the following categories:
• Water Resistant Plasterboard - This type of plasterboard are best suited to be used in water areas like bathroom, laundry rooms and kitchens.
• Acoustic Plasterboard - Due to its sounding proofing qualities, this type of plasterboard is preferred to be used in home theatres or noisy areas.
• Flexible Plasterboard - This is to be incorporated on curvy surfaces.
• Fire Resistant Plasterboard - Just like the name implies, this type of plasterboard is best suited for use in high fire hazard areas.
If you’re about to kick start some small renovations around your house or office, using a plasterboard to clad your walls is a very simple and worthwhile task. However, if you want to do major renovations or need to apply plasterboard to your ceiling, the best option would be to leave it to a seasoned professional.
Usually, slipperiness is caused by algae or dirt on top of the deck or terrace. A full cleaning treatment should restore the natural grip of the wood or stone. If slipperiness is a persistent problem, consider installing grip mats in high traffic areas of the deck.
Yes, your shed does need a base. This is to give it a solid, level foundation. Open soil will not help with the longevity of the shed itself or the contents within. The best materials to use to make your shed base are concrete, natural stone or wood.
- Tongue and groove timber boards
- Boards for the ledges and braces, at least 20mm thick
- Nails
- Hammer
- Saws, including a circular saw
- Chisel
- Mallet
- Cut your boards to size If you can’t buy boards at the right height and width for your door, cut the boards to length using a circular saw. Don’t forget to sand and treat any cut ends with timber preservative. Lay out the boards in the best arrangement for your shed door, with the inside of the door facing up.
- Arrange the ledges and braces On most shed doors, you’ll probably need 3 boards across the back of the door to form the ledges. The ledges keep the door straight and keep the boards of the door together. The braces are the parts of the door that slope down to form a ‘Z’ shape between the ledges. Ensure that the braces are sloped up from the bottom and middle hinge to stop the door from sagging as the timber expands and contracts in the weather. Once you’re happy with the arrangement, mark the spots on the boards where they will meet and cut out of the housings using a chisel and mallet.
- Put the door together Use clamps to pull the boards together and hold the ledges and braces in place. Nail from the front of the door through the boards and ledges to fix them. Secure the ledges and braces with screws; you may want to pre-drill and countersink holes to prevent the wood from splitting. Remember to treat them with preservative if you do.
- Fix the shed door hinges Make sure you measure carefully before attaching the hinges, ensuring you know where the pin sits in relation to where the door opens.
- Treat the door and add locks and handles Apply some wood oil, like linseed or teak oil, to help prevent water damage. Then add locks or handles to your shed to help keep it secure. If you’d rather leave it to the professionals, there are plenty of specialists that will be able to make a shed door for you, or even put up an entire shed.
If you’re thinking about making improvements to your home, it’s only reasonable to become familiar with the ins and outs of the requirements to make the project a success. Not just the cost involved to complete the project, but also the duration it’ll take to complete the job and lots more. When it comes to the installation of wooden flooring, there’s a need to find out whether or not an underlay is required for the task. In this article, we’re going to consider this in order to ensure that you’re on the right track. Let’s take a look!
First and foremost, underlays are common with carpets as they allow for an even surface with no lumps and bumps. It also provides a deeper barrier between the carpet and the floor as carpets, themselves, aren’t particularly thick enough to provide adequate comfort when walking on them. Underlay also helps improve insulation which in turn, helps cut down your energy bill. So, are underlays also needed with wooden flooring?
In general, wooden flooring does not really need an underlay. This is due to the fact that they’re perfectly comfortable to walk on without the need to add an extra padding underneath. However, the subfloor will have to be made prior to the installation, as a result, an underlay is needed at all there. With that in mind, it’s highly recommended to make use of an underlay when installing a boarded floor to a wooden subfloor mainly due to the fact that it’s able to provide a much-improved insulation. When it comes to wooden flooring, it’s always best to go for quality rather than looking for ways to cut corners. If you’re able to go for the best project with professional installation and little extras like undelay, you’d notice and enjoy the long lasting nature of your wooden flooring immediately after installation.
Carpenter help and advice
How it works
Tell us about your Carpenter project
Answer a few quick questions to help us match you with the right Carpenter
Get up to 4 free quotes
Receive no-obligation quotes from 4 Carpenters working in Settle.
Pick the right pro for you
Compare prices, customer reviews and services, and hire the right Carpenter.
Are you a Carpenter in Settle?
View our open Carpenter jobs near you
Join today