Yes, your shed does need a base. This is to give it a solid, level foundation. Open soil will not help with the longevity of the shed itself or the contents within. The best materials to use to make your shed base are concrete, natural stone or wood.
Find a Carpenter you can trust in Fort Augustus.
Choose from 61 Carpenters, all rated by people like you.
Over 21 reviews & an average rating of 4.5/5 stars, you'll find the right pro
Choose and shortlist
Use the shortlist button to select up to 4 tradespeople, enter your project details and press send
Keen to get on with the job?
Get up to 4 quotes from local Carpenters near you
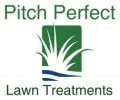

Pitch Perfect Laens
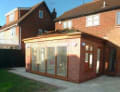

K&D joinery
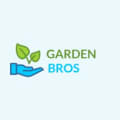

Garden Bros
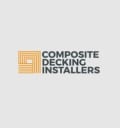

Composite Decking Glasgow
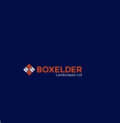

Boxelder Landscapes
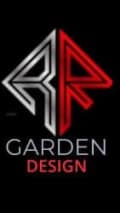

Hutchison garden services
How much do Carpenter services cost?
Do you have a need for a carpenter in or around your house? If yes, then one of the first things you’d probably want to know is the exact amount it would cost to get the project over the line. Now, carpenters are skilled craftsmen that are able to make things with wood and fabricate all sorts of wood constructions. The price charged by carpenters are determined by a wide range of factors which makes it nearly impossible to provide a short and accurate estimate without having a look at your unique requirements. In this post, we’re going to give you an in-depth insight into general carpentry charges while also considering some of the influencing factors. Let’s take a look!
Some of the most common factors that determines the price charged by a carpenter includes the project type, the size as well as scope of the project, the location of project, ease of access, experience and qualification of the carpenter and lots more. For instance, if the job is a minor one such as building a shed, it’ll cost a lot less than something more complex which requires a bit more experience like constructing a staircase. In general, building a shed will have a labour cost within the range of £150 to about £250, while a staircase construction will require a labour cost in between £1,000 to £1,500. For general carpentry, you can expect to pay within the range of £20 to £30 hourly rate depending on a number of factors which are stated above. It’s also important to state that while some carpenters charge per hour, others by the day and several of their projects will be charged at fixed prices.
The table reveals the kinds of work that Carpenters normally do and also the regular cost range of these jobs. Some tasks take longer to finish than others so costs do differ by task.
View our Carpenter cost guide View our Carpenter adviceThe average price
of a Carpenter in Fort Augustus is:
£879
Carpenter job | Carpenter cost in 2025 |
---|---|
Kitchen Fitting in Fort Augustus | £975-£2,495 |
Carpenters and joiners in Fort Augustus | £375-£575 |
Plasterboard dry lining in Fort Augustus | £638-£978 |
Wood flooring in Fort Augustus | £750-£1,150 |
Wooden decking in Fort Augustus | £1,125-£1,725 |
Garden shed in Fort Augustus | £450-£690 |
Wooden window repair in Fort Augustus | £320-£480 |
Carpenter FAQs
- Start in one corner of the sub-frame and position the first board across the inner joists. You want the deck board in the opposite direction to the inner joists, ensuring that it’s flush with the frame. Position any end-to-end joins between the deck boards halfway across an inner joist so you can screw both boards into the joist for stability. Make sure you keep a gap of between 5-8mm to allow for expansion of the wood.
- Begin to screw your deck boards to the joists. You’ll need to secure the deck board to every joist is covers along your deck frame. Use two screws for every joist. Mark where you’re going to add your screws, ensuring that they are at least 15mm from the end of the board and 20mm from the outside edges. Drill pilot holes for the screws, being careful to only drill through the deck board and not the joist. Then screw the decking screws into the holes.
- Continue to screw in the deck boards, ensuring you leave the correct expansion gap. You can stagger the deck board joins across the deck for more strength.
- Sand down any cut ends if you need to before applying decking preserver to protect the timber from rotting.
Check your Price's door installation cost calculator and charges guide will allow you to estimate both typical labours only costs for door hanging & installations, renovations and repairs as well as the total estimate for comprehensive door installation projects.
• Door & Frame Installation Job and the average Cost in £'s
• uPVC door installation including glazing & architrave costs around £90 per door
• uPVC french & patio door sets including glazing & architrave costs around £120 per pair
• Softwood french & patio door sets including architrave costs around £180 per door
• Hardwood french & patio door sets including architrave would cost around £250 per pair
• Softwood internal door hanging only would be around £40 per door
• Hardwood internal door hanging only would set you back around £48 per door
• Softwood external door hanging only is around £60 per door
• Hardwood external door hanging would cost around £70 per door
• Locks, letterboxes & door furniture timber doors are around £15 per Item
• Glazing £15 per pane
• Brick cut-outs single doors is around £60 per cut-out
• French or patio door brick cut-outs will be around £90 per cut-out
• New lintels will cost around £150 per lintel
Door Repair Costs and Charges
Estimate door mending labour charges by totalling the unit costs of the mandatory jobs. The complete door repair cost includes the total labour charge plus the cost of all parts, fixtures and fittings. A call out charge may be added on jobs totalling less than £100.
Average Cost of Door Repair Job
Replacement glazing units for uPVC doors will be around £15 per unit
Replacement glazing units for timber doors is around £20 per unit
Replacement door glass pined & putty will cost£30 per pane
Replacement handles are around £10 each and general repair work will cost you £25 per hour
Building & FENSA certificate charges
FENSA certificates are obligatory for maximum door replacements and new build setting up prices differ from council to council.
Average Cost of Window Repair Job: One to two doors will cost around £85
Average Cost of Door Fixtures & Fittings Removal Job
Removing internal doors will cost around £10
Removing internal door liners will cost around £15
Removing external timber doors will cost about £10
Removing External timber door frame will be around £20
Removing external uPVC door & frame removal will be around £30 and Rubbish disposal will cost £150 per ton.
Being the primary material used in wooden flooring installation, the floorboards are the main supply costs. With that in mind, you should also know that there are a large variety of wooden flooring types to select from, each with their unique pros and cons which should all be considered before making a purchase decision. If you’re looking to get the supply cost of wooden flooring in the UK, then you’ve come to the right place! Here is a basic price guide of various and some of the most popular types of floorboards.
If you wish to go for an engineered wood flooring, this looks better when compared to laminate and is more affordable than solid wood. You can expect to pay within the range of £20 to about £100 per square metre for this wood flooring type.
Laminate flooring, on the other hand, is also quite cheap, easy to install and quite hardwearing, however it tends to warp over time as a result of exposure to moisture and it also happens to be the least attractive of all the other flooring types. You can expect to pay within the range of £10 to about £50 per square metre for this wood flooring type.
Solid wood flooring is a great option with a better look and feel to it. However, it also tends to warp over time and more difficult to install as against laminate. You can expect to pay within the range of £20 to about £100 per square metre for this wood flooring type.
Parquet flooring is long lasting and very attractive, but quite expensive to have fitted. You can expect to pay within the range of £25 to about £200 per square metre for this wood flooring type.
After making the decision to install a new wooden flooring in your home, the next obvious step is finding the right installer to get the job done. When a wooden floor is fitted and properly maintained by the right professional, it will not only outlive the owner but also survive several generations. As a result, finding the perfect installer for your task should be a top priority to get the best return on investment. Here are a few sources that will put you in the right direction to finding a reliable wood flooring installation company.
• Friends, Relatives & Neighbours
If you have a friend, relative or neighbour that has a wooden floor installed in their homes, you can go for a visit to check out the work done. If you’re pleased with the work done, you can proceed to ask about the work ethics of the installer and get the contact if satisfied.
• Store Contact Lists
You’ll discover a long list of wooden flooring contractors on many stores trading flooring materials. These installers may not be affiliated with the store owners, but many stores see it as their responsibility to point you in the right direction so that the flooring material acquired from them can be put to good use.
• Internet
With the rapid rise of online technology, there’s hardly a service you can’t find on the internet. Websites like HomeAdvisor have been helping people find their desired service providers with relative ease for so long. To get the right installer online, it’s advisable to check reviews as well as testimonials before moving forward. Nowadays, you’re most likely going to find so many positive online reviews as some businesses now go to the extent of dubiously writing good reviews for their companies. As a result, it’s recommended to pay closer attention to the negative reviews and check if it’s something you can cope with before hiring an installer for your wooden flooring.
Click here to learn more about wood flooring.
The cost of wood flooring varies by the type of wood and by the finish required. As a guide though oak solid wood flooring cost about £35 - £45 per m2. The average wooden cost by material are approximately £40 per m2 for pine, £45 per m2 for cherry, £60 per m2 for maple and £75 per m2 for walnut. This price does exclude the laying of the flooring and the underlay required.
- Plan your shed base
You must have a sturdy base for your shed, otherwise the frame won’t stand properly and could stop the door from opening. Decide whether you’re going to have:
- A concrete base laid on hardcore
- Concrete slabs on sharp sand
- Treated wood beams on hardcore or shingle
- An interlocking plastic system
- Treat wood with preservative To help your shed last as long as possible, you should coat all the wooden parts with timber preservative before you put it together.
- Put the shed floor together Some will need more assembly than others, but you need to make sure that the floor panel is attached to the joists; follow the manufacturer’s instructions for the correct spacing.
- Put up the shed walls
- Mark the centre point of each wall on its bottom edge, then do the same for the shed floor so you can line them up together.
- Stand the gable end on the base and line it up. Check that it’s vertical with a spirit level – you might need someone to support the panel while you do this. Use a temporary holding batten to keep it in place.
- Fix a side panel to the gable end panel with countersunk screws, then add the second side panel in the same way.
- Fit the roof
- If the shed comes with a support bar, put this in position before you put the roof panels in.
- Nail the roof panels in place, ensuring there’s a parallel and equal overlap at each end.
- Roll out some roofing felt from front to back, leaving a 50mm overlap at each side. Secure it with clout-headed felt tacks at 100mm intervals.
- Apply mastic sealant to the outside corners, then fix each corner trim with 30mm nails.
- Add the fascias and finials, predrilling 2mm holes to avoid splitting the wood. Nail them through the felt into the shed using 40mm nails.
- Add the shed windows
- Slide each windowsill into the tongue and groove cut out, then put the window cover strip in position, fixing it to the vertical framing.
- From inside the shed, put the glazing sheets into the window rebates, making sure the bottom edge of the glazing sheets sit on the outside of the sill.
- Fix the window beading on the top and sides with 25mm nails.
- Fix the walls to the floor Before you do anything, make sure you check that the centre marks on the walls line up with the marks on the shed floor. Then fix the wall panels to the floor with 50mm screws, aligning them with the joists. And that’s it! But if you’re not confident in building a shed yourself, there are plenty of professionals available who will be happy to help.
- Place a post in the corner of the frame you created with the pegs and string. Measure and mark out 100mm from each side.
- Dig out this soil to a depth of 700mm (watch out for cables or pipes). You should have a 300 x 300mm hole. Repeat for the other 3 corners.
- Using a brick bolster, split a concrete block in two. Put a section of the block in each hole.
- Get a length of post longer than you need and place one in each hole. You can cut it down later.
- Create props on each post to hold them in place until you’re ready to add a cement mix. Check that they’re level. When you’re happy that they are, secure them in place with a concrete mix, making sure you create a slope in the concrete so that rainwater runs away from each post. When the concrete is set, remove the props.
- Create a string line around each corner post and find the centre point between each. Place a timber batten at each point, ensuring that they’re not spaced any more than 1500mm apart.
- Working from the corner where the deck will be at its highest above ground level, measure and mark on the post where the highest part of the frame will be.
- Measure from the far side of one post to the opposite and cut sections of joist to size. Line up a piece of joist with the mark you made and temporarily secure it. Factor in a 2mm fall for every metre of decking so rainwater can run off.
- Secure the frame to the other corner post, ensuring it’s at the right level. Do this for every side of the outer frame.
- Using 100mm coach screws with washers hanging on the end, secure each end of the four sections of frame.
- Mark out where the centre of the support posts will be and secure all of these posts to the frame, except the centre post.
- Add your central support joists. These should run in the same direction as the deck boards will run. You’ll need to measure from the inside of the frame on one side to the inside of the frame on the opposite side. Attach the joist in the same way as you did for the other posts. Repeat so the centre post is in between two sections of frame and secure the posts with concrete.
- Trim down all the posts to the correct height using a saw.
- Add your weed-control fabric and weigh down with gravel across the entire area.
- Measure 400mm from the centre of the outer frame and mark a line. This will be where the first joist is positioned. Repeat at 400mm intervals down the length of the frame – if the last one will be more than 400mm, add another joist to create enough support.
- Attach a joist hanger to each end of the joist.
- Place the joist in position so the centre lines up with the 400mm spacer mark.
- Secure using external grade screws once you’re happy that the joist is flush with the frame.
Carpenter help and advice
How it works
Tell us about your Carpenter project
Answer a few quick questions to help us match you with the right Carpenter
Get up to 4 free quotes
Receive no-obligation quotes from 4 Carpenters working in Fort Augustus.
Pick the right pro for you
Compare prices, customer reviews and services, and hire the right Carpenter.
Are you a Carpenter in Fort Augustus?
View our open Carpenter jobs near you
Join today