Usually, slipperiness is caused by algae or dirt on top of the deck or terrace. A full cleaning treatment should restore the natural grip of the wood or stone. If slipperiness is a persistent problem, consider installing grip mats in high traffic areas of the deck.
Find a Carpenter you can trust in New Tredegar.
Choose from 139 Carpenters, all rated by people like you.
Over 102 reviews & an average rating of 4.2/5 stars, you'll find the right pro
Choose and shortlist
Use the shortlist button to select up to 4 tradespeople, enter your project details and press send
Keen to get on with the job?
Get up to 4 quotes from local Carpenters near you
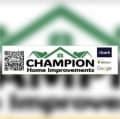

Champion Home Improvements
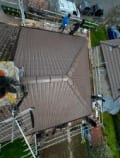

J & D Home Improvements
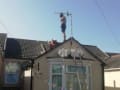

BGD Building and Roofing
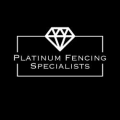

Platinum Fencing Specialists


Multi trade home solutions


The Grass Master
How much do Carpenter services cost?
Do you have a need for a carpenter in or around your house? If yes, then one of the first things you’d probably want to know is the exact amount it would cost to get the project over the line. Now, carpenters are skilled craftsmen that are able to make things with wood and fabricate all sorts of wood constructions. The price charged by carpenters are determined by a wide range of factors which makes it nearly impossible to provide a short and accurate estimate without having a look at your unique requirements. In this post, we’re going to give you an in-depth insight into general carpentry charges while also considering some of the influencing factors. Let’s take a look!
Some of the most common factors that determines the price charged by a carpenter includes the project type, the size as well as scope of the project, the location of project, ease of access, experience and qualification of the carpenter and lots more. For instance, if the job is a minor one such as building a shed, it’ll cost a lot less than something more complex which requires a bit more experience like constructing a staircase. In general, building a shed will have a labour cost within the range of £150 to about £250, while a staircase construction will require a labour cost in between £1,000 to £1,500. For general carpentry, you can expect to pay within the range of £20 to £30 hourly rate depending on a number of factors which are stated above. It’s also important to state that while some carpenters charge per hour, others by the day and several of their projects will be charged at fixed prices.
The table reveals the kinds of work that Carpenters normally do and also the regular cost range of these jobs. Some tasks take longer to finish than others so costs do differ by task.
View our Carpenter cost guide View our Carpenter adviceThe average price
of a Carpenter in New Tredegar is:
£943
Carpenter job | Carpenter cost in 2025 |
---|---|
Kitchen Fitting in New Tredegar | £975-£2,495 |
Carpenters and joiners in New Tredegar | £375-£575 |
Plasterboard dry lining in New Tredegar | £638-£978 |
Wood flooring in New Tredegar | £750-£1,150 |
Wooden decking in New Tredegar | £1,125-£1,725 |
Garden shed in New Tredegar | £475-£1,595 |
Wooden window repair in New Tredegar | £320-£480 |
Carpenter FAQs
Considerations
If you're thinking about making changes around your household that include working with wood, you ought to hire a local carpenter. Looking to fix a loose piece? Or looking for some drastic improvements? A carpentry expert might be the top choice.
General carpenters are expert woodsmen and know a variety of areas from grounds to gear. Maximum carpentry depends on a rudimentary set of skills which your worker may choose to build upon by specialising. For example, few carpenters have a talent for wood repair, building original constructions or manufacturing furniture.
Time
The extent of time it takes to complete a certain project is another consideration to be kept in mind. This is particularly essential if you are on a constricted timeline or dealing with time limitations. Most carpentry projects take about 13 hours to finish. Although, this is purely dependent on the intricacy of the project and the pre-arranged timeline you and your carpenter agree to.
The cost to hire a general carpenter in the UK amounts to £20 to £25 per hour on an average. Though, it is always imperative to speak with a professional in carpentry services about this.
General Carpentry Costs in the UK:
• National Minimum Cost is £20
• National Maximum Cost is £25
• The national average is around £22
Cost Comparison of Popular Carpentry Services in the UK (Average Hourly Rate):
• Furniture Refinishing is around £17
• A Cabinet Repair is around £23
• Finish Carpentry will set you back a minimum of £30
• General Carpentry is around £20
• Fine Woodworking is about £20
Carpentry is a brilliant method to improve your household and to help maintain its visual pleasantness. Finding a decent carpenter at the correct value is a vital area that needs undivided attention in terms of your project. Whether you're reinforcing your staircase or looking for a total renovation of the house that would change its look, a general carpenter will complete your project to the highest standards.
What Is Plasterboard?
The plasterboard is unarguably one of the most common building materials across the globe. Sometimes referred to as gypsum board, gyprock, drywall or wall board, the plasterboard is mostly incorporated for ceiling cladding and interior walls in several homes and offices in recent times. However, despite its global acceptability, it’s a very misunderstood building material.
The plasterboard is manufactured using a gypsum core with a heavy paper covering both sides of the sheet. The measurement of a standard plasterboard sheet is a length of 2.4 metres in and a width of 1.2 metres, with a thickness of about 13mm. The board usually have either a bevelled or a bit flat edge. The bevelled edge makes it easy for the installers to use a plaster to smooth out the surface after nailing the sheets to walls and ceilings as well as taping the edges.
The plasterboard comes in different types. Although various manufacturers provide a unique name for their products, but they’re all included in one of the following categories:
• Water Resistant Plasterboard - This type of plasterboard are best suited to be used in water areas like bathroom, laundry rooms and kitchens.
• Acoustic Plasterboard - Due to its sounding proofing qualities, this type of plasterboard is preferred to be used in home theatres or noisy areas.
• Flexible Plasterboard - This is to be incorporated on curvy surfaces.
• Fire Resistant Plasterboard - Just like the name implies, this type of plasterboard is best suited for use in high fire hazard areas.
If you’re about to kick start some small renovations around your house or office, using a plasterboard to clad your walls is a very simple and worthwhile task. However, if you want to do major renovations or need to apply plasterboard to your ceiling, the best option would be to leave it to a seasoned professional.
- Mark out the area and dig the top layer of soil, trying to get the ground as flat as possible.
- Build a timber frame to size.
- Measure out 4 rows of 3 blocks to create good weight distribution and lay in place.
- Underneath each block, dig around 50mm wider than the blocks and about 150mm deep. Fill the hole with pea gravel until it’s flat.
- Place timber planks along the rows of blocks and see how level it is. Add or remove blocks where necessary. If it’s only a small difference, use shingle underneath the timber until it’s level.
- Nail your timber shed base to the timber planks to create a sturdy base for your shed.
Yes, although you should make sure that the terrace or decking is able to support the weight of a hot tub. Usually, you will need to have a structural survey carried out on the area. Seek the advise of a hot tub retailer or installer about the logistics of installing one at your property.
How To Lay Wood Flooring
Laying of wood flooring is actually a very simple task contrary to many beliefs. First and foremost, before commencement of the fitting process, you must determine the direction you would like the engineered wood flooring to lie in. To do this the right way, they should lie in the direction of the the longest wall. However, if your subfloor is wooden, then having the boards positioned across the joists underneath would be your best bet to get started.
Here are some simple steps to follow to properly lay your wood flooring:
• Start from a corner, working from left to right and place the initial rows of the boards with the groove’s end directly opposite the closest wall.
• Make use of expansion spacers. Place them in between the wall and the board alongside an expansion gap of about 8 to 10mm.
• Place the board’s final rows at about 100mm wide. To achieve this, it is crucial to be pro-active with the measurement and cut the boards (if you deem fit) to adjust the first row.
• With the help of the click system, the boards will click together.
• Fit in the next board. Ensure to attach the tongues together (30 degrees from the floor) and once done, you can proceed to lower and lock it in place. Do this till you get to the end of the row.
• Cut the last board of the row to size if its too long.
• If the part cut off is up to 300mm, simply use it to start the next row. If not, cut a new board in half to use.
• Put the rows side by side in such a way to ensure the joints are staggered at each and every row. Keep a consistent gap between the wall and the planks via the continuous use of the spacers.
• Lay a plank over the last row to determine the width of the previous board. Position a new plank in a way that its tongue is directly against the wall. Once done, proceed to mark a line of plank underneath to get the required width. Then, fit the plank into the space with the help of a pull bar and hammer.
Click here to learn more about wood flooring.
- What you need the shed for
- How much space you have
- How big you need the shed to be
- Which style of roof you want
- What material you would like
- How big your budget is
- Hand-crafted from Nordic White Spruce
- Felt roof reinforced with high-grade polyester
- Tongue and groove cladding makes it more weatherproof so ideal for items that must be kept dry
- High eaves for more head height and to store taller items
- Pent roof and fixed windows allow lots of light
- Ideal for putting up against a wall or fence
- Door can be hinged either side
- Ideal for small gardens or those with fewer tools to store
- Apex roof for water runoff
- Tongue and groove walls
- Tall floor-to-gable door
Carpenters are involved with numerous diverse kinds of construction, from home improvement to cabinet making, and framing to large construction projects.
Since the start of time, men have utilised hand tools to make things. You need to understand the correct usage of a hand saw, hammer, plane, screwdriver, and other manual tools. These tools are used to attach ready pieces and produce a complete product, such as nails, screws, and dowels (pre-formed fragments of wood that fit into pre-drilled holes), which are then fastened and amassed.
Carpenters must be adept with the safety and proper usage of numerous power tools, including the ones that do the cutting, shaping, and refining of the wood. This permits constituents to take the arrangement desired for a specific project. Some of these tools include large table saws and drills, band saws and sanders. Apart from power tools, there are also tons of power hand tools including saws and hand drills that can help with the smaller details of any project.
Cabinetry and Furniture Making
Being a cabinet fabricator or furniture maker gives you the chance to build purposeful devices for a home. You need to be able to plan cabinets, chairs, tables, and other products, frequently to fit into a provided space. It is up to you to pick the proper material such as wood, metal, or fabric, and then make the decision about the type of stain or paint, and also the necessary hardware needed to attach the cabinets and complete the furniture.
Residential Carpentry
Looking to become a residential carpenter? Your primary work would be on home improvement and other repair projects; indoors and outdoors. Residential carpenters complete setting up projects on wood flooring, outdoor decks, and patios. This job requires you to design your projects and then work on those designs. You also have to be skilful at work with your client base of proprietors, who you have to satisfy both aesthetically and financially, by keeping costs in check.
Carpenter help and advice
How it works
Tell us about your Carpenter project
Answer a few quick questions to help us match you with the right Carpenter
Get up to 4 free quotes
Receive no-obligation quotes from 4 Carpenters working in New Tredegar.
Pick the right pro for you
Compare prices, customer reviews and services, and hire the right Carpenter.
Are you a Carpenter in New Tredegar?
View our open Carpenter jobs near you
Join today